Highlights and Recap of the 2022 Lean Production Special Activity
Intelligent manufacturing is a new type of manufacturing that applies the new generation of information technology, such as big data, Internet of Things (IoT), cloud computing, and artificial intelligence (AI), throughout the entire life cycle of the manufacturing process. The goal of intelligent manufacturing is to achieve personalized, flexible, high-quality, and low-energy consumption manufacturing. To realize intelligent manufacturing, Lean Production and Quality Engineering are always essential. Lean Production is both the foundation and the goal of intelligent manufacturing. The objective of intelligent manufacturing is also to make production leaner.
In April 2022, our company launched the Lean Production Special Improvement Activity, which was led by the engineering department and with the broad participation of various departments. Based on the central idea of “returning to basics and consolidating the foundation”, this activity aims to enhance relevant processes through serial and sustainable special improvement initiatives, collect and establish accurate and reliable data, build a fair and transparent lean site, demonstrate the real effects of lean improvement, and thus achieve a lean culture of “full participation, strengthened management, continuous improvement, and quality casting.”
1. Return to Basics
Adhering to the principle of return to basics, first, persist in lean improvement for the purpose of achieving the proper state; second, ensure data transparency and accuracy.
The proper state includes:
? The proper state of people: Full participation, not causing trouble for others/next process.
? The proper state of machines: Restoration of appearance and performance, achieving small-scale automation, reducing employee labor intensity.
? The proper state of materials: Qualified upon production.
? The proper state of procedures: Complete and perfect standards.
? The proper state of environment: Temperature, humidity, ESD, etc.
Data transparency and accuracy includes:
? Takt time: Set based on optimized bottleneck processes.
? Line balance rate: Designed by bottleneck process, eliminating wait waste to achieve maximum production efficiency.
? Inspection and test nodes (FTY): Triggering Fail with any defects, strictly recorded in the MES system as required.
? Precise task output rate: Timely completion of tasks within 0-3 hours.
2. Consolidate the Foundation
To consolidate the foundation, efforts will be focused on improving the single-piece flow rate in production and on-site 5S improvements, to comprehensively establish the foundation of lean production.
The improvement of single-piece flow rate combines production processes such as assembly, testing, packaging, and warehousing into a single flow, monitors and analyzes the single-piece flow rate, identifies bottleneck processes and focuses on improvement, ensuring production continuity and effectively improving the single-piece flow rate.
? Takt Time: Develop a reasonable production takt time based on customer TT.
? Standard WIP: Set a standard WIP for each workstation and implement a mechanism to stop the line and improve operations if the standard WIP is exceeded.
? Line Design/Transformation: Implement lean Cell lines and design line bodies suitable for single-piece flow production.
? Maintenance Management: Mechanize operations and continuous improve to maintain single-piece flow production.
? Horizontal Deployment: Replicate the single-piece flow production mode across all assembly, testing, packaging, and shipping line systems.
On-site 5S improvement measures include:
? Sorting: Useful/Useless, Red-Tagging, and Static/Dynamic Images.
? Straightening: Item classification, Three Fixed Management (material handling, quantitative determination and location) Management, and Dynamic Visual Management.
? Sweeping: The three source activities, the F-sign operation, and the spot inspection benchmark book.
? Cleaning: Standardization.
? Sustaining Disciplines: Habitualization.
3. Highlights
(1) LCIA Application - Automatic Screw Machine
Before improvement: Manual screwing by employees, which caused high work intensity and the risk of missing or improperly placing screws.
After improvement: Introduction of automatic screw machine to reduce employee workload, and avoid issues with missing or incorrectly placed screws.
(2) LCIA Application - Automatic Gluing
Before improvement: Manual gluing by employees, resulting in high work intensity, low production efficiency, and failure to meet 5S standards.
After improvement: Introduction of automatic gluing machines to reduce employee workload, improve efficiency and meet 5S standards.
(3) LCIA Application - Automatic Weighing
Before Improvement: Weighing station operators manually handle products and scan them by scanning guns, requiring more than 2,300 scans per shift, with high repetition and fatigue.
After Improvement: Introducing LCIA mechanisms, the weight of the products is automatically measured and sorted after passing the scanning process; the cylinder will push the product through the slide track to the next process, achieving automation in the weighing process.
(4) Integrated Fiber Optic Testing Device
Before improvement: After testing each product in the testing station, the fiber optic head needs to be cleaned, but the cleaning cloth was too far from the detection head, resulting in a large range of motion (M5 action).
After improvement: An integrated testing device is utilized where the cleaning cloth fixture and tester are connected, reducing operator range of motion from M5 to M3 and eliminating the need for manual adjustment after each test.
(5) Introduction of Automatic Conveyor Belt at MP9 Station
Before improvement: The test section transported the product by slide rails, which easily scratched the product. There was a high risk of collision and damage during testing with multiple MP9 test modules.
After improvement: The product is transported by an automatic conveyor belt, and the fixture is tilted at a 15-degree angle to eliminate the need for operators to raise their arms when taking out the board, avoiding product friction with the antenna module that could cause defects.
(6) Improvement of FQC On-site Spot Checking Station
Before improvement: After the spot checking of FQC, the product needs to be sent back to the checking station, with cross-process operations.
After improvement: The spot checking station has been moved to the front of the production line, with slide rails added for product transfer to eliminate process crossover and unnecessary transportation waste.
4. Summary
Through the 2022 Lean Production Special Activity, the following achievements were obtained:
(1) UPPH reached its established goals. The practical experience of improving single-piece flow rate promoted to all production lines, improving efficiency and quality.
(2) A batch of automated equipment was introduced, including Automatic Pulse Welding Machine, Air-blowing Screw Machine, Automatic Dispensing Machine, Wi-Fi Calibration Automation Equipment, Automatic Nozzle Cleaning and Detection System, SMT Board Labeling Machine, and Empty Box Automatic Recycling Device, which saved manpower and improved efficiency.
(3) Gradually formed the lean culture of “full participation, strengthened management, continuous improvement, and quality casting”.
(4) An IT-based improvement proposal system was developed, which allowed employees to fill in improvement suggestions by scanning QR codes with their mobile phones, facilitating more people to participate in improvement activity. Hundreds of proposals were collected, and the full-staff proposal improvement activity continued to be promoted.
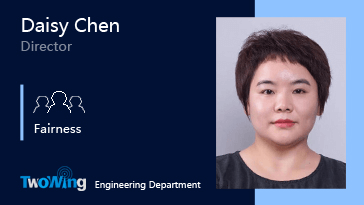